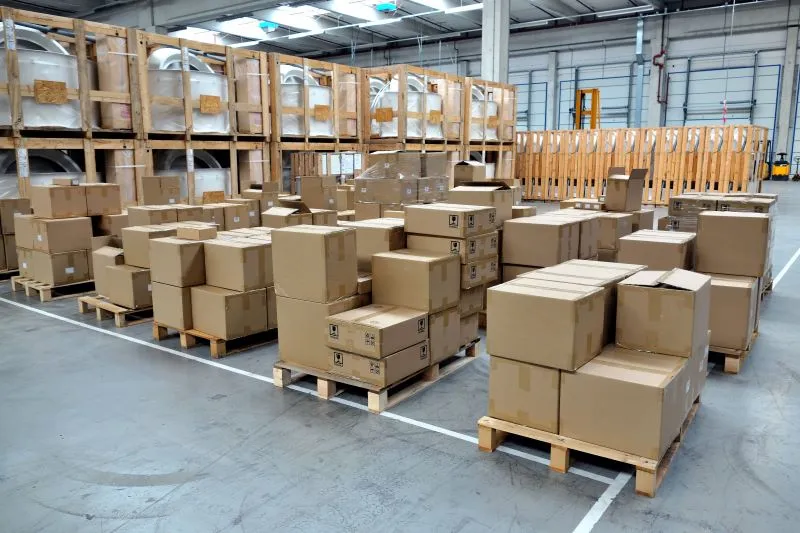
『パレタイズ』とは、荷物を輸送・保管するためにパレットに整理して積み付けていくことです。積み方の種類は「パレットパターン」と呼ばれます。
近年、物流量の増加、人手不足などから、安全に、効率よく荷物を運ぶ方法が求められます。
本記事では、パレタイズのメリットや、パレットパターンについてご紹介します。
パレタイズとは
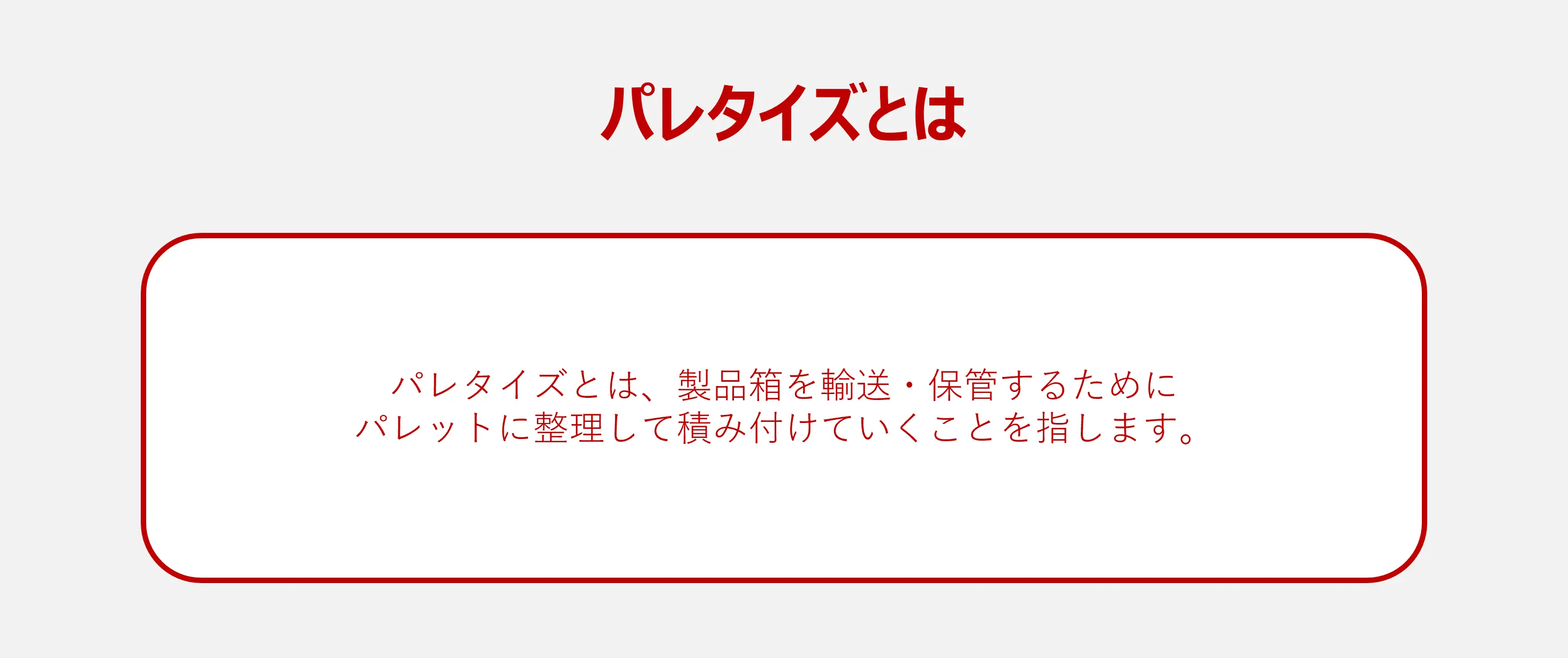
『パレタイズ』とは、荷物を輸送・保管するためにパレットに整理して積み付けていくことを指します。対して、パレタイズした荷物を開梱しパレットから取り出す作業は、『デパレタイズ』と呼ばれます。
パレタイズされた荷物は、フォークリフトでまとめて運搬することや、パレット単位で整理・管理することができます。パレタイズが必要な荷物の多くは、箱や袋、プラスチックケースなど、個包装された状態で、積み重ねることができます。
パレット自体も荷役・輸送・保管の効率化に役立ちますが、注意点として、 箱の強度や内容物の確認が必要です。荷崩れ防止のため、最後にベルトやストレッチフィルムで固定する場合があります。
対して、そのまま輸送ラインに乗せる場合は、『ばら積み』と呼ばれます。
例えば、流動性のあるもの、壊れやすい品物、または特殊な形の品物などの積み重ねられないものの場合、パレタイズできないため、効率性は落ちてしまいます。
「パレタイズ」は「ばら積み」に比べて、人件費、作業効率、トラックの待機時間短縮など、経費削減に役立ちます。
パレタイズのメリット

荷崩れを防ぐ
荷物を整理しパレットに積み付けて しっかりと固定することで、フォークリフトでの移動中や運送中の荷崩れや破損のリスクが低くなります。
入出庫の検品等の精度向上
パレットごとに整理された荷物は、入出庫の際、検品等が簡素化することで精度があがり、時間も短縮されます。パレタイズパターンによっては、温度管理が厳しい荷物でも対応できます。
また、荷物ごとの積み付けを決めることで、管理がしやすくなります。
トラックへの積み込み、荷下ろし時間の短縮
パレタイズされたパレットは、フォークリフトによる積み込みや荷下ろしが短時間でできることや、パレットの大きさから積み込める量、重量を予想できるため、運送計画が立てやすい点もメリットです。
今後、「2024年問題」のドライバー等の人手不足が考えられる為、大きな効果が見込めます。
パレタイズのデメリット
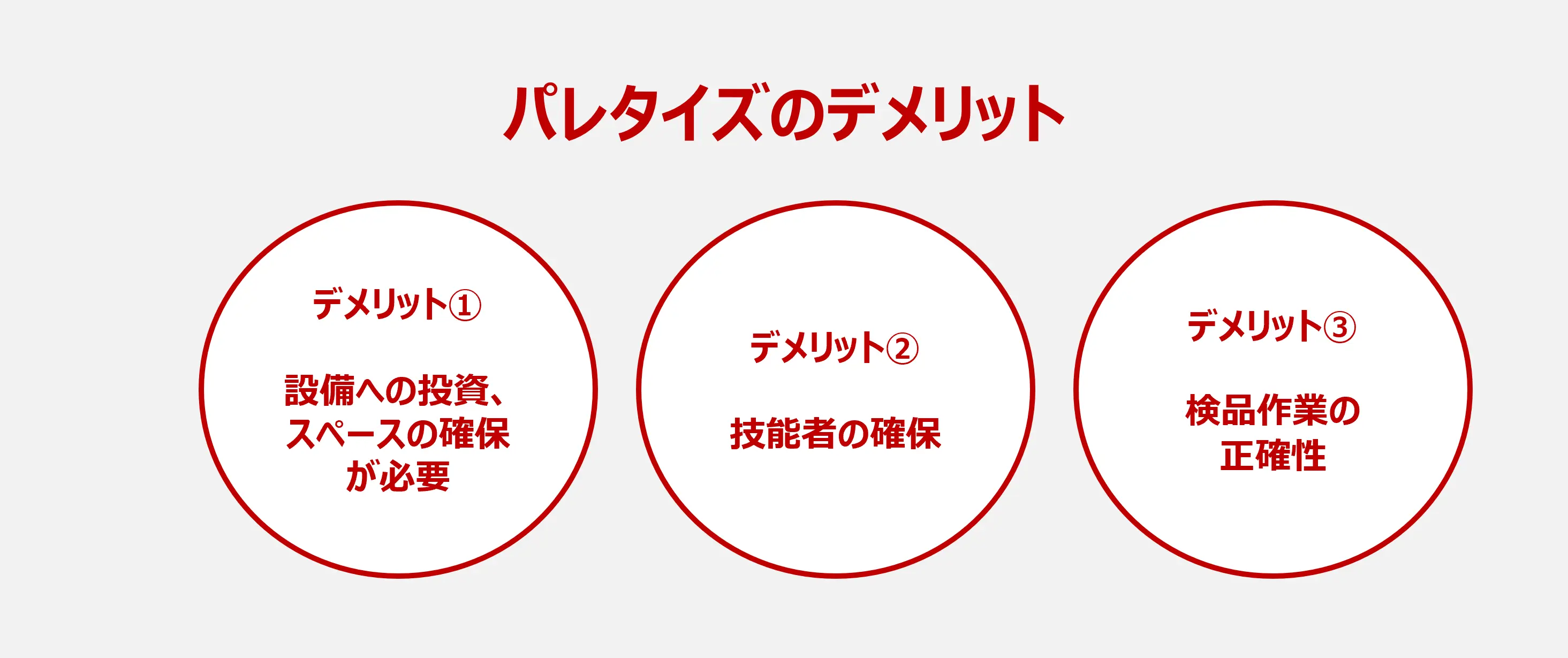
設備への投資、スペースの確保が必要
設備として、フォークリフトやパレットの購入、作業するためのスペースの確保が必要となります。
また、パレットの枚数も大量に必要となるため、投資金額が大きくなります。
技能者の確保
フォークリフトを使用する場合、敷地内であっても、操縦するには「フォークリフト運転特別教育修了証」または「フォークリフト運転技能講習修了証」が必要となり、スムーズに積み込むためには、経験値や技量も必要となります。
検品作業の正確性
パレタイズ後の修正などを防ぐため、検品作業の正確性が求められます。
その為、知識や経験不足では時間を要し、さらに人的ミスの発生も考えられます。
積み分けパターン(パレットパターン)
積み方の種類は「パレットパターン」と呼ばれます。
荷崩れしないよう、安全にパレタイズするためには、積み方(パレットパターン)がポイントとなります。
荷物の積み方によって、安定性や耐圧性が変わるため、適切な積み付けが大切です。
積み付けの種類(パレットパターン)を紹介します。
ブロック積(平積み)
工業荷物や日用品など、一般的な荷物を常温で輸送するコンテナで、最も普及している積み方です。
積み込まれる荷物には電化荷物、自動車部品、コーヒー、たばこ、ワインなど多岐にわたります。ただ、上に行くほどバランスが悪くなるので、積み上げる高さに注意が必要です。
交互列積み
1段ずつ荷物の向きを90度変えて積んでいく積み方です。
ブロック積みよりも横向きの力に強く、荷崩れしにくいメリットがありますが、荷物の形によって90度向きを変えたときに縦横の寸法が合わない場合、全体の形として正方形にならないため、パレットからはみ出す恐れがあり、時には間隔の調整が必要です。
レンガ積み
1段の中に横向きと縦向きの荷物が混在している積み方です。
1段ごとに荷物の向きを180度変えることで、荷崩れしにくくなります。倉庫に納品する際も、さまざまな角度から荷物を目視できるため、確認しやすくなりますが、形が長方形になりやすいため、正方形のパレットの場合、積みにくくなる場合があります。
スプリット積み
レンガ積みの応用パターンとしてスプリット積みがあります。
横向きの荷物の間に隙間(スプリット)を設け、全体の形を整える方法で、ダンボールの縦横比が合わなくても、隙間で調整できるため、さまざまなサイズのパレットに合わせることができます。しかし、その隙間から荷崩れを起こしてしまう可能性があるため、パレットの内側に隙間を設ける必要があります。
ピンホール積み(風車形積み付け)
荷物を風車のような形に積み上げていく積み方です。
荷物の向きを反転させて積むことで、横向きの力に耐性がある。パレット中央部分に穴ができ、冷蔵や低温輸送などの温度管理が厳しい荷物の場合に向いていますが、その空洞のせいで積載率が下がってしまうデメリットがあります。
ダブルピンホール積み
ピンホール積みの応用型で、中央の穴を2つにした積み方です。
パレットの上にピンホール積みをしたら、その内の1つの荷物を使って、もう1つピンホール積みを構成し、残った角の部分にも荷物を置きます。これを左右反転させながら積んでいく積み方です。積み方が複雑なので、スムーズに積めるまで時間がかかりますが、積載性が高いのでパレットに1つでも多く荷物を積みたい場合には有効です。
以上のほかにも積み方パターンは色々とありますが、荷物に合った積み方が必要となります。
パレタイズを効率化する方法
上述したように、安全にパレタイズ作業するためには、荷物のサイズや特性に合わせたパレットパターンを選ぶことが必要だということを解説しました。では、その他にも安全かつ効率的にパレタイズする方法はあるのでしょうか。
パレットの積み方を工夫する
パレタイズの際、最も重要なのは荷崩れによる事故を起こさないことです。以下の点に注意しながら、常に「フォークリフトで運んだ際、荷崩れしないか」、「トラックで輸送しても安全か」を念頭においてパレタイズしましょう。
- ・荷崩れをしないようにすること
- ・適切なパレットパターンで積むこと
- ・荷崩れの原因となるオーバーハングに注意すること
パレタイズの自動化
数量間違い、積み忘れ等のミスや、事故発生のリスクは工夫により軽減できます。例えば、マニュアル化やパワードスーツの導入、環境改善などを通して、パレタイズ・デパレタイズにおけるミスを抑え、効率的な運用が多くの企業で実施されています。
しかし、どれだけ工夫や対策をとっても完全に、人的なミスをゼロにすることは難しく、パレタイズの自動化が解決策の1つとして挙げられます。
長時間にわたる重労働を行えば、疲労によって数量間違えや積み忘れ、荷物を落としてしまうリスクだけでなく事故発生のリスクがあります。
しかし、ロボットを使用し自動化をすれば、ミスなく正確なパレタイズが実現できます。導入コストはかかりますが、一度パレタイズするラインを構築してしまえば、ランニングコストやこれまで発生していたリスクによるコストを抑えることが可能です。
パレタイズの課題解決はLOGITOまで
今後、深刻な「2024年問題」を迎え、深刻な人手不足が加速しています。
労働力をカバーしていくためにも、物流作業の効率化、自動化、省人化、DXは急務となります。
LOGITOでは、パレタイズ関連業務の効率化を実現するために、国内外問わずさまざまなメーカーと連携し、御社に最適なご提案が可能です。
マテハン機器の導入、パレタイズでは、バンニング、デバンニングシステムも今後を見据えての導入に、課題解決にむけてワンストップでコーディネート致します。
以下の資料では、パレタイズにかかわる具体的なソリューションをご紹介していますので、ご関心のある方はぜひご覧ください。
LOGITO 運営事務局
LOGITO 運営事務局では、全世界17カ国34拠点のグローバルネットワークにて培ったノウハウを生かし、物流自動化に関するトレンド・業界動向からノウハウ、成功事例まで、物流自動化の実践に役立つ様々な情報をお届けします。