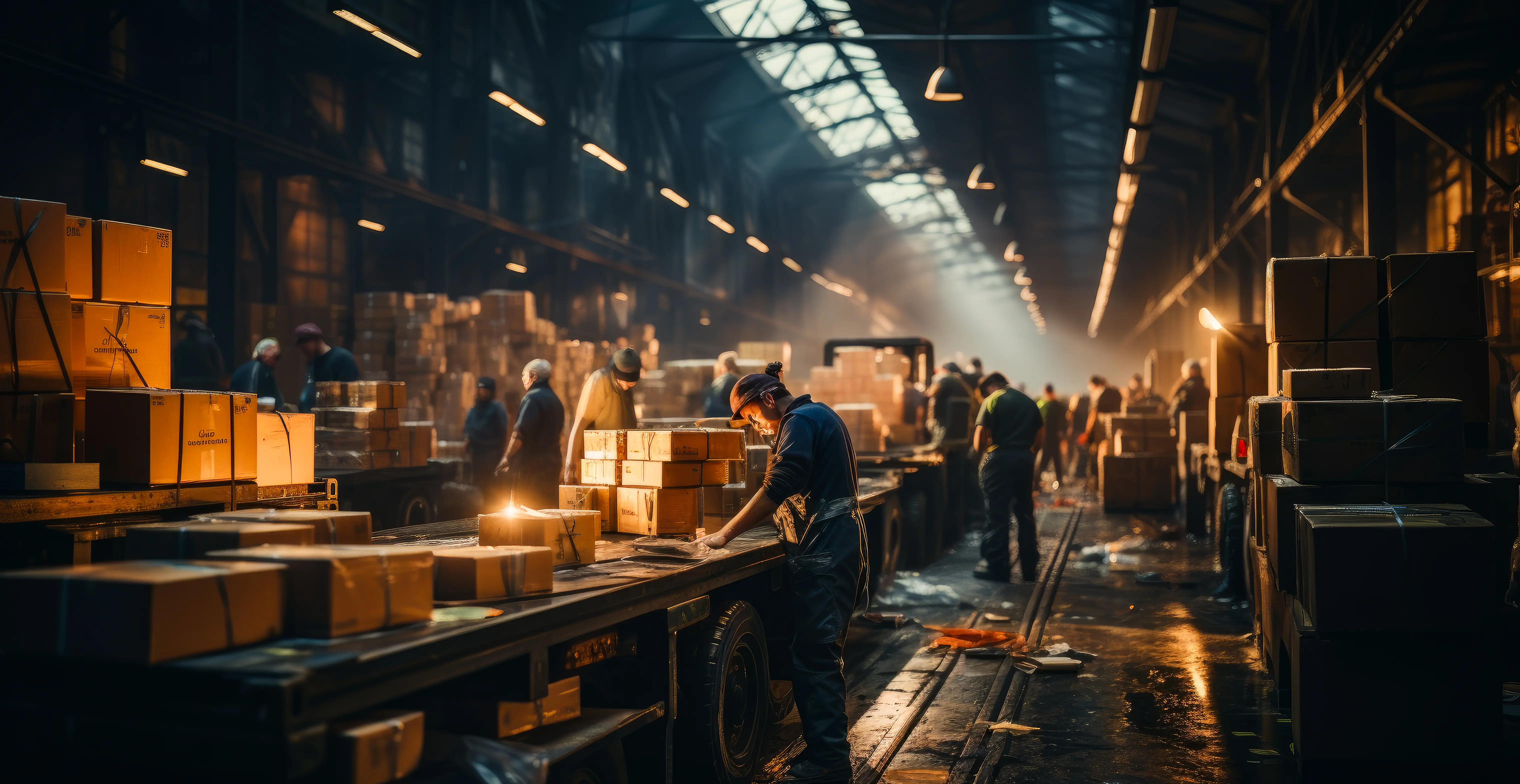
工場内での資材や部品、完成品などの移動を「構内物流(工場内物流)」と呼びます。構内物流(工場内物流)は必要なときに必要なモノを必要な数量搬送することが求められ、工場全体の生産性向上を左右する重要な要素です。本記事では、製造業・倉庫業の省人化の変遷や、工場の構内物流の省人化に取り組むメリットを解説します。
構内物流とは
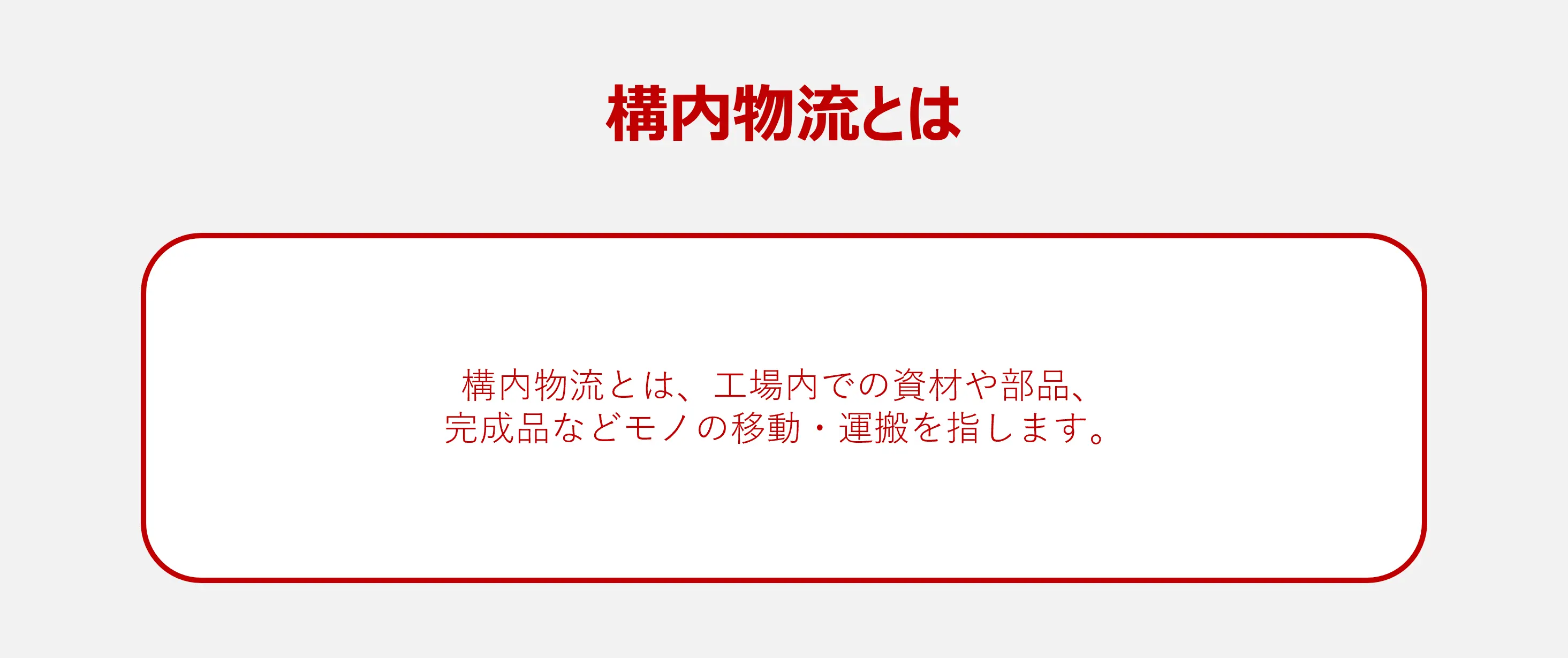
構内物流とは、工場内での資材や部品、完成品などモノの移動・運搬を指します。構内物流(工場内物流)は、必要なときに必要なモノを必要な数量搬送することが求められ、工場全体の生産性向上を左右する重要な要素です。なお、構内物流は「工場内物流」とも呼ばれています。
以下では、構内物流(工場内物流)について詳しく解説しています。
次章では、構内物流における省人化の変遷について紹介します。
製造業・倉庫業の省人化の変遷
物流の省人化は、テクノロジーの発展によって
4つのイノベーションが起こっており、現在は、
AI・
IoTによる省人化や自動化が取り組まれた「ロジスティクス
4.0」の時代が到来しています。ロジスティクス
1.0からロジスティクス
4.0までの変遷を解説します。
ロジスティクス1.0大量の物資をスピーディーに輸送できるようになったことを「ロジスティクス1.0」と呼びます。第一次産業革命によって、人が都市にある工場へ集まり、大量生産が行われたことで、従来の交通手段では輸送に時間がかかっていました。しかし、鉄道や船舶に関する技術が普及したことによって、多くの貨物を短時間で目的地に運べるようになりました。
ロジスティクス2.0
第二次世界大戦後の荷役作業の機械化を指します。もともとは軍需品の補給を効率化するために使われていたフォークリフトですが、戦後、物流には欠かせないパレットの普及も相まって、急速に荷役作業の機械化が進みました。
ロジスティクス3.0
1980年代の物流管理のシステム化を意味します。産業革命以降の機械化によって、物流業界に大きなイノベーションが訪れましたが、積み込みや取り卸しといった現場作業までしか自動化は進んでいませんでした。たとえば、荷物の入出管理や在庫管理などに関する業務は人手に頼ったままで、すべて書類と台帳によって管理されていました。
1980年代に入るとコンピュータの普及に伴い、管理・処理業務に「WMS」が導入されました。倉庫内の物流管理の正確さを高め、入荷・格納・ピッキング・検品・梱包までの作業状況などをトータル管理するシステムとして活用されています。
ロジスティクス4.0
AI・IoTといった新技術により、これまで人が行ってきた作業をロボットが行うようになり、省人化・自動化がさらに加速すると予測されます。
今まで人間でなければできなかった「人の判断や操作」といった作業の機械化により、物流オペレーションの主体が人からIoTやAIなどの新技術に置き換わろうとしているところです。これまで人間が担っていた作業を機械に置き換えれば、人手不足の解消に役立ち、需要増加への対応とコストの削減が可能になり、従業員の待遇向上にも繋がります。
このように製造業・物流業の省人化は進んできましたが、現代で省人化が求められる背景を次章で解説します。
製造業・物流業の省人化が求められる背景
物流の省人化が求められる背景の1つとして、人材不足が挙げられます。今後はシニア層や外国人労働者など、幅広い雇用を広げる必要性があり、作業負担の軽減や作業者の能力に依存しない物流現場を作っていく必要があります。
工場の構内物流の省人化に取り組むメリット
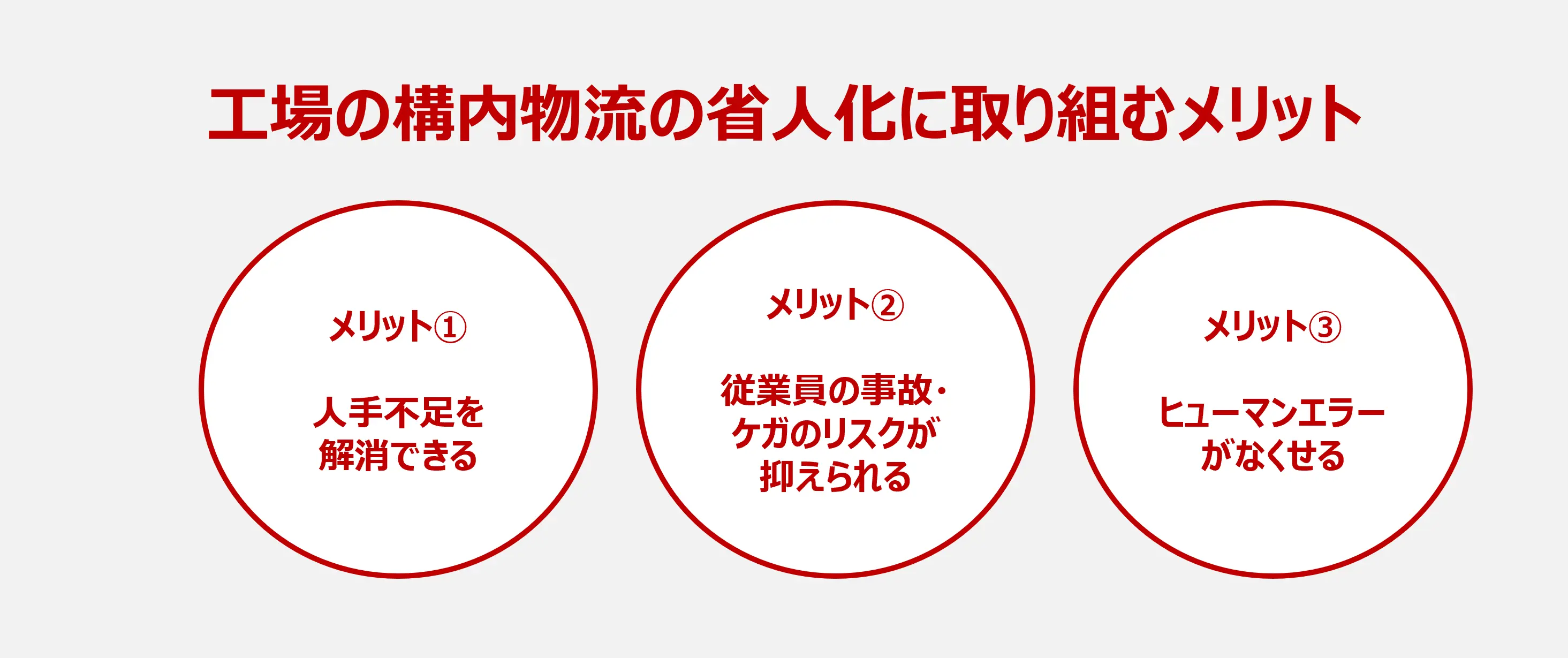
工場の構内物流の省人化を進めることによるメリットとしては、人による作業の削減による人手不足の解消、人による作業が少なくなることで、従業員の事故・ケガや、ヒューマンエラーのリスクを防止が挙げられます。
人手不足を解消できる省人化により、人が作業することが少なくなります。ロボットは時間制限がなく稼働してくれるため、人手による作業も削減できます。
従業員の事故・ケガのリスクが抑えられる
ロボットや機械が作業を行うため、重い荷物を運んで転んだ・フォークリフトとの接触事故が発生したなどのリスクを防止できます。
ヒューマンエラーがなくせる人の作業ではどうしてもヒューマンエラーが発生してしまいますが、ロボットであれば無くすことができます。 また、ロボットが作業することで作業のばらつきが生じないため、効率化といった観点でも大きな効果があります。
工場の構内物流の省人化を成功させるポイント
工場の構内物流の省人化に取り組む上で、「導入・維持コスト」・「想定していた効果が出ない」などの課題が挙げられます。 費用対効果を出すためには、まず自社の工程の流れを確認することが重要です。たとえば、工場では、生産工程と構内物流の工程が入り組むことで複雑なフローになっているケースがあり、多くの無駄が発生しています。
次章では、構内物流の省人化の導入事例を紹介します。
導入事例-YKKAP株式会社様
YKK AP株式会社様はYKKグループの建材事業の中核会社として、窓・サッシ等の住宅建材を主力に、ビル建材等の設計、製造、施工および販売を手掛けている、国内アルミサッシのトップメーカーです。
AGV・システム導入前の状況
社内の物流センターにおいて、窓枠の組み立てに使う小部品の種類が多いため、従来使用していた棚に置ききれず、パレットや棚以外の場所で保管するため、移動距離が伸び、業務効率の低下や身体的負担が生じていました。 また、一部の作業者のみが保管されている場所を把握しているため、管理が俗人化されてしまい作業時間のばらつきが出ていました。 これらの現場課題に加え、今後加速する作業者不足の懸念もあり、自働化による作業の効率化・平準化を目指し、試験的に自働化システムを導入することになりました。
導入システムのイメージ
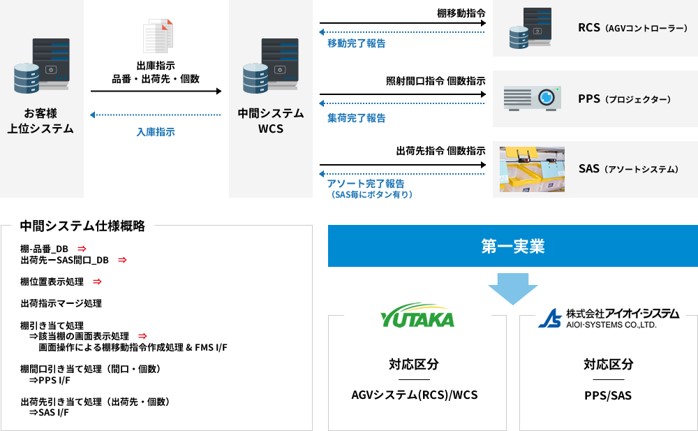
AGV・システムの導入後、作業者負担の軽減と属人化していた作業の平準化を実現
システムの導入により、大きく2つの効果が認められました。
①作業者が長い距離を歩く必要がなくなり業務効率や身体的負担を軽減
②俗人化していたピッキング作業の平準化が進み、誰でも作業可能
このように、導入検討当初に設定した改善目標を達成することができ、これ以外にも作業ミスを未然に防ぐ効果もあり、作業環境は大幅に改善されました。
YKKAP株式会社様で導入されたソリューションについて、以下の資料にて紹介しています。
構内物流(工場内物流)の省人化はLOGITOまで
第一実業では、製造業や倉庫業等の企業様向けに物流の自動化を図るソリューションサービス「LOGITO」を提供しています。自動倉庫やAMR(自律走行搬送ロボット)などの各種ソリューションをお客様の課題に合わせた形でご提案しており、構内物流(工場内物流)の改善を支援します。
また、工場内の現場分析から機器・設備のコーディネート、据付後のアフターフォローまでワンストップでご支援しており、国内外のグループ会社との連携により迅速かつ最適なソリューションを提供することで、工場内の搬送作業における省人化を効果的に実現します。
以下の資料では、物流の自動化をはじめ構内物流(工場内物流)を改善するための具体的なソリューションをご紹介していますので、ご関心のある方はぜひご覧ください。
LOGITO 運営事務局
LOGITO 運営事務局では、全世界17カ国34拠点のグローバルネットワークにて培ったノウハウを生かし、物流自動化に関するトレンド・業界動向からノウハウ、成功事例まで、物流自動化の実践に役立つ様々な情報をお届けします。