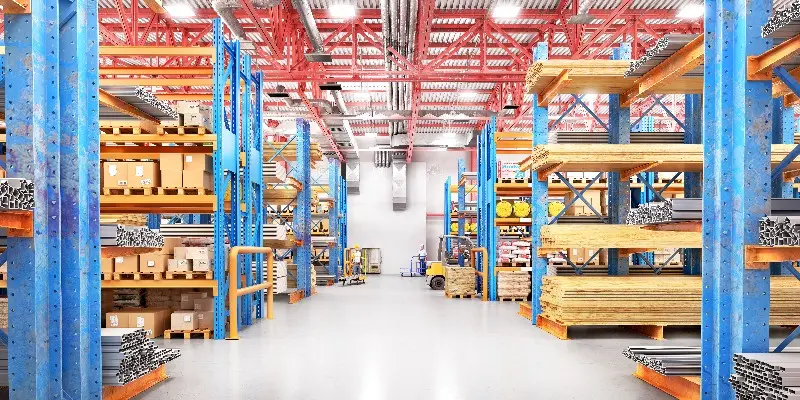
構内物流や倉庫における保管業務は、注文後のスムーズな出荷を実現するうえで非常に重要な工程です。しかし、スペースが有効活用できていなかったり、作業導線が非効率になっていたりするケースが多くあります。そこで本記事では、倉庫の保管効率を高める管理方法や課題解消のヒントなどをご紹介します。
構内物流の省人化において以下のお悩みはございませんか?
- 省人化に取り組んだが、うまく効果がだせなかった
- 各メーカーが同じような製品を扱っており、強みがわからない
- 各工程間の搬送に課題がある
上記のようなお悩みごとがございましたら、LOGITOをご検討ください。LOGITOは製造業や倉庫業等の企業様向けに、物流の自動化・省人化を図るソリューションサービスです。
知識と経験が豊富な総合機械商社だからこそ、自動倉庫やAMR(自律走行搬送ロボット)、ロボットアーム等の導入を低コストで実現します。
「構内物流の省人化を進めたいが、進め方が分からない。」などといったお困りごとがあれば、以下ページでLOGITOの構内物流の省人化を実現するサービスをご紹介しておりますので、ぜひご覧ください
構内物流・倉庫作業における保管とは
構内物流業務における保管とは、倉庫内で商品や材料などを預かり、適切に管理することを指します。 入庫した製品や材料を在庫として、出荷されるまでの間所定の場所にて管理され、注文に応じて発送されます。
保管業務の目的
構内物流業務における
保管の一番の目的は需給調整です。通常、商品を製造してから販売するまでにはタイムラグがあります。注文が入ってから生産していたのでは間に合わないため、材料・仕掛品・完成品を適切に管理し、注文に応じてすぐに出荷できる体制を整えておかなければなりません。そこで保管という工程が不可欠となります。
保管は製造業や倉庫業、小売り、ECビジネスなど、さまざまな業種に共通する工程であり、構内物流全体の効率性や品質に影響するため、決められた場所で商品を預かり、品質や数量を適正に管理する必要があります。
物流倉庫で保管が重要視される理由
保管は、入出荷を行う前後で経由する重要な物流工程であり、特に以下の理由から重要視されています。
素早く出荷できるよう数量や品質を正しく在庫管理する
保管が重要視される理由は、
決められた納期に合わせスムーズに出荷できるよう、在庫商品の数量や品質を正しく管理する必要があるからです。 単に商品を倉庫に置くだけでは、保管としては不十分です。必要な商品を必要な数量だけ、適切なタイミングで出荷するために、何を、どこに、どれだけ保管しているのか正しく把握しておく必要があります。
このように効率的な出荷を行うために重要となるのが、以下でご紹介するロケーション管理です。
保管作業で重要な3つのロケーション管理方法
商品を保管する場所を「ロケーション」と言います。ロケーション管理とは、
棚の番号や段、間口などにより割り振られたロケーションを用いて、商品を管理する方法です。
商品の保管場所をロケーションという「住所」によって区分することで、何が、どこに、保管されているのか誰でも把握しやすくなります。
ロケーション管理には、主に以下3つの方法があります。
固定ロケーション
固定ロケーションは、
決められた場所に商品を保管する管理方法です。
ロケーション番号に従って機械的に格納するため、経験の浅い従業員でも作業しやすく、現物管理もしやすいというメリットがあります。一方で、商品ごとに決められた保管場所を確保しないといけないため、新商品が加わると保管場所を増やしたり、在庫の数量や商品の種類の増減などに応じてレイアウトを変更したりする必要があり、保管効率が悪くなる点がデメリットです。
フリーロケーション
フリーロケーションは、
保管場所が決められておらず、空いている場所に適宜保管する方法です。
空いているスペースに保管していくためスペースを無駄にせず、保管効率が高いというメリットがあります。しかし、保管場所が決まっていないがゆえに、各商品の保管場所を都度覚えなければならず、システム化しないと適切な保管が困難な点がデメリットです。また、同じ商品が別々の場所に保管されているケースも多く、管理効率が下がってしまいます。
ダブルトランザクション
ダブルトランザクションは、
固定ロケーションとフリーロケーションを併用したハイブリットな方法です。
ポイントとしては、倉庫内をストックエリアとピッキングエリアに分けることにあります。ストックエリアではフリーロケーションでスペースを有効活用し、ピッキングエリアでは固定ロケーションで作業することで、移動距離短縮などの作業効率アップを図れます。
保管作業でよくある課題
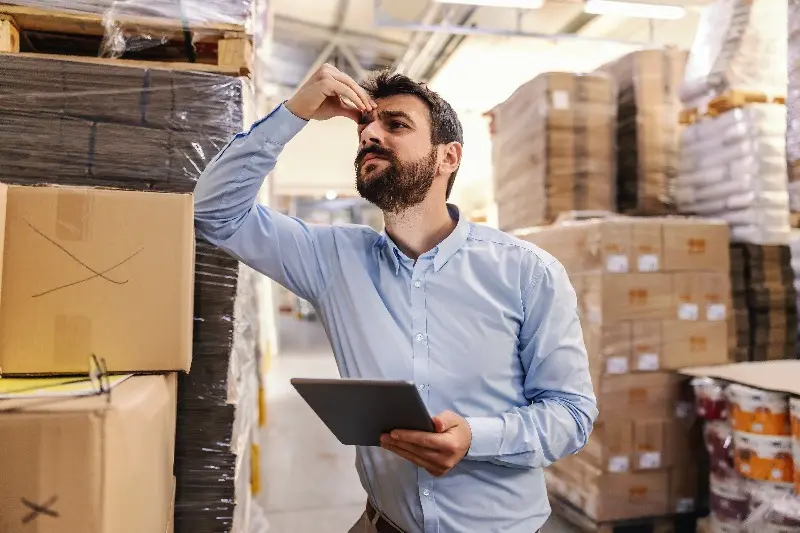
保管作業では以上のようなロケーション管理を行いますが、保管場所の把握や効率的な導線の確保など、適切なロケーション管理ができていない場合、以下3つの課題が生じます。
スペースの有効活用ができていない
先述の固定ロケーションの場合は特に、スペースを無駄にしてしまっているケースがあります。商品が置かれていない空間ができていないか、ラックなどに無駄なく商品を積み上げられているか、また商品と商品の間に隙間ができていないか、といった点をチェックし、
保管スペースを見直すことが重要です。
入庫や出庫の作業が効率的に行えていない
ロケーション管理自体は的確にできていても、出荷頻度の高い商品が倉庫の奥にあるため、ピッキング時の移動距離が長くなり、作業効率が下がっていることもよくあります。
出荷頻度に応じて保管場所を変更・修正し、
無駄のない作業導線にする工夫が大切です。
状況の変化に対応できていない
商品ごとの季節や繁忙期・閑散期など扱う商品の変化などによって保管する商品への変化への柔軟性が求められます。また、製造業であれば、工程のレイアウトや機械の配置が変わることもあり、
状況の変化に対応できず、作業が非効率になったり保管場所を間違えたりするリスクを考えなければなりません。
そのため、工程レイアウトの変化に対応するために、ロケーション管理は重要になり、WMSを活用して最新の状況や工程を従業員に遅滞なく周知することで、保管する商品や工程レイアウトの変更時もロケーションを考慮することができます。
このような課題を踏まえ、以下では保管作業を効率化する2つのソリューションをご紹介します。
保管作業を効率化するソリューション
LOGITOでは製造業や倉庫業等の企業様向けに、物流の自動化を図るソリューションサービスを提供しています。保管業務を効率化するソリューションとしては、自動倉庫とWMSの2つがあります。
自動倉庫
自動倉庫とは、商品や部品の入庫から保管、出庫までの一連のフローを一元管理して自動化するためのオートメーションシステムです。
複数の梱包形態やさまざまな部材・製品の保管に対応しており、商品の出し入れを行うスタッカークレーンや昇降リフター、コンベア、無人搬送車などを組み合わせて、
倉庫の自動化・省人化を実現し、保管量の増大も可能です。
WMS
WMS(Warehouse Management System)は、倉庫管理を行うソフトウェア・アプリケーションです。
ロケーション管理といった倉庫で行われる業務のマネジメントをデジタル化することで業務標準化を行います。さらに、
作業を見える化することで無駄な作業やスペースを発見し、効率的な保管業務に役立てることもできます。
LOGITOでは、保管以外の物流工程の自動化も推進しております。
以下資料では、物流自動化におけるノウハウをまとめたお役立ち資料もございます。
物流工程の自動化でお悩みの方は併せてご覧ください。
LOGITO 運営事務局
LOGITO 運営事務局では、全世界17カ国34拠点のグローバルネットワークにて培ったノウハウを生かし、物流自動化に関するトレンド・業界動向からノウハウ、成功事例まで、物流自動化の実践に役立つ様々な情報をお届けします。