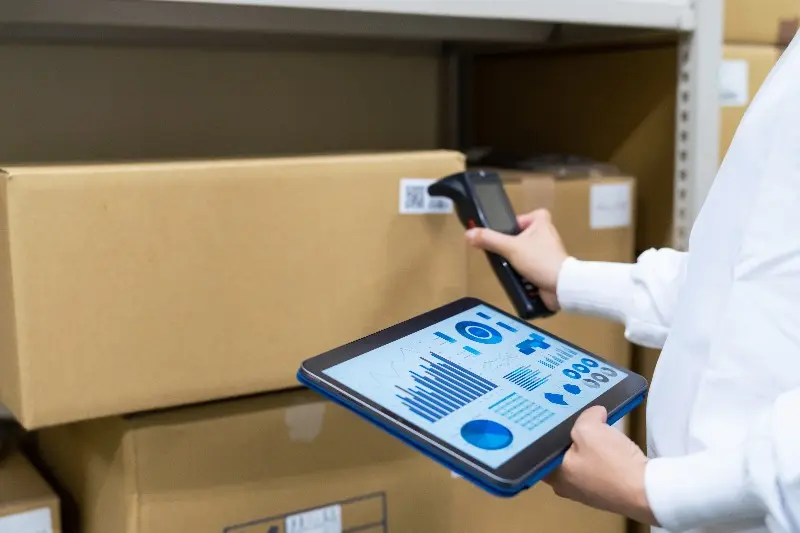
誤出荷・誤納品はお客様からの信頼を失ってしまうため対策が必要です。誤出荷・誤納品が発生する原意は「誤品」・「数量・入数ミス」・「出荷指示ミス」の3つであり、それぞれに対して適した対策が必要です。本記事では、誤出荷・誤納品の各原因について説明したうえで、その対策方法について解説します。
誤出荷・誤納品が発生する3つの原因
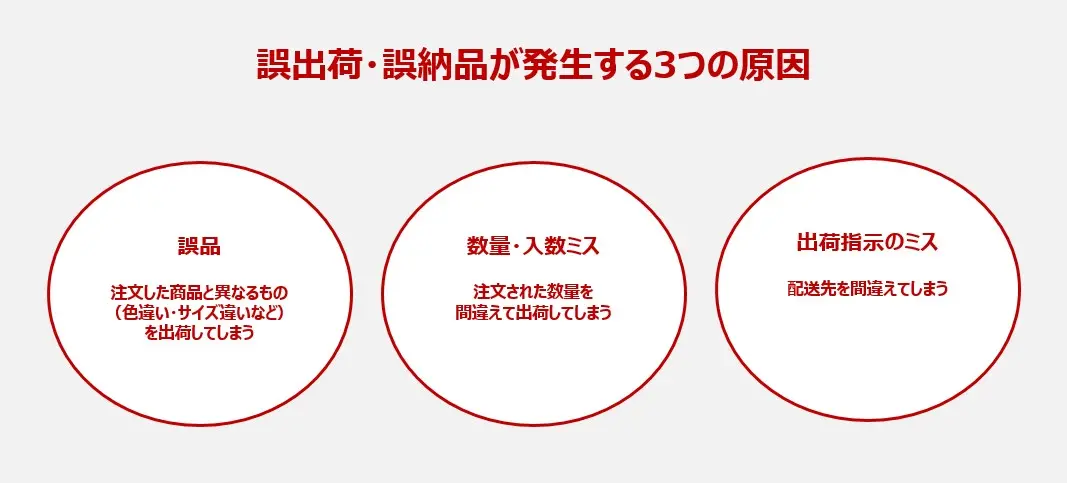
物流業務における誤出荷・誤納品は、信頼性やブランドイメージの低下に加え、再送といった作業工数・コスト増加につながることから、できる限り減らさなければなりません。そのためには
誤出荷・誤納品の発生原因を把握し、それぞれに対策を講じることが大切です。
誤出荷の原因は以下3つがあります。
- 誤品:注文した商品と異なるもの(色違い・サイズ違いなど)を出荷してしまう
- 数量・入数ミス:注文された個数を間違えて出荷してしまう
- 出荷指示のミス:配送先を間違えてしまう
以下ではまず、それぞれの誤出荷の原因について見ていきます。
誤品が発生する原因
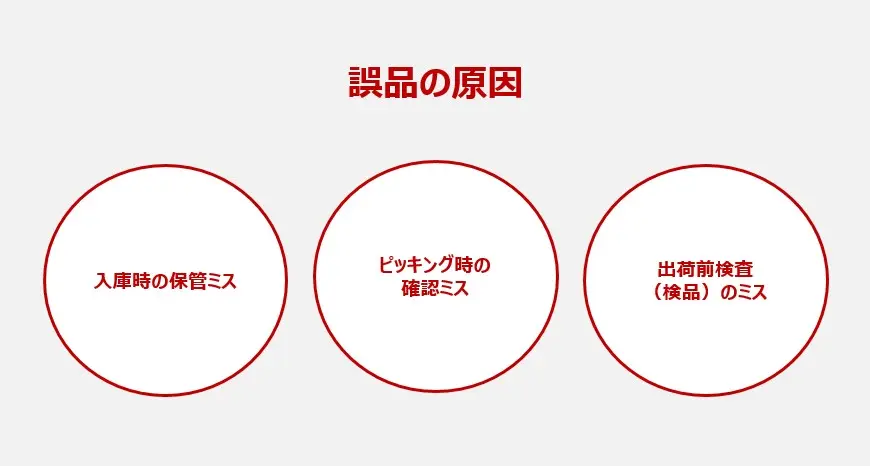
誤品の原因は、大きく分けて入庫時の保管ミス、ピッキング時の確認ミス、出荷前検査(検品)でのミスという3つがあります。
入庫時の保管ミス
商品が入荷した際に、
保管場所を間違えてしまうことで誤品が起きるパターンです。誤った場所に保管してしまうと、ピッキングの際に間違えに気づかず出荷してしまうことがよくあります。
入荷した商品と保管場所の対応関係がわかりやすいロケーション管理を行うことが重要です。
ピッキング時の確認ミス
ピッキング時における、
ピッキングリストの確認ミスにより発生する誤品です。どの場所にどの商品があるのかについて、従業員の経験に頼ってしまっている場合によく見られます。
また、商品名や商品番号が似ているものや、カラーやサイズのバリエーションが多いものなどは特に注意が必要です。
出荷前検査(検品)
入庫時やピッキング時にミスが発生しても、出荷前の検査(検品)でミスが発覚すれば誤品を防ぐことができます。しかし、出荷前検査が目視の場合、すべてのミスを発見することは難しく、
出荷前に検査したにもかかわらず誤品が起きることがあります。
数量・入数ミスが発生する原因
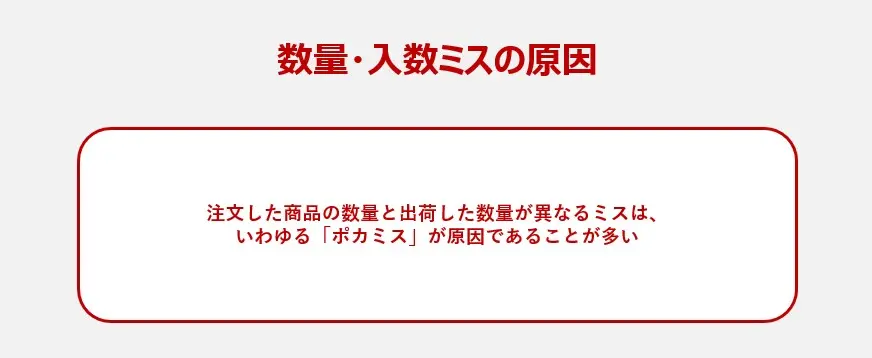
注文した商品の数量と出荷した数量が異なるミスは、いわゆる「ポカミス」が原因であることが大半です。
ポカミスによる誤数
数量のポカミスとしては、同じ商品の購入数が多いときなどに数え間違えたり、数量の桁を読み間違えたりするケースなどが考えられます。
また、「1個」と「1ケース」など、注文単位をうっかり間違えてしまうパターンもあります。新人だけでなく、ベテランでも慣れていくうちに確認が甘くなりポカミスをしてしまう可能性もあり、
人が作業している限り完全になくすことはできません。
出荷指示ミスが発生する原因
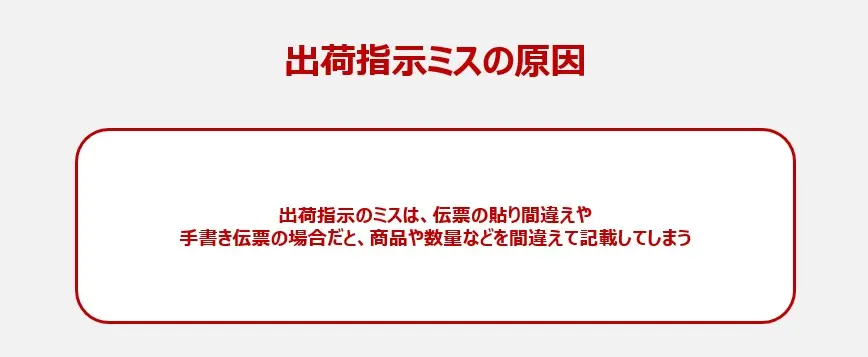
出荷指示のミスは、送り状伝票が他の商品の納品書と一緒になってしまい、
別の梱包物に貼り間違えることで起きることがよくあります。複数の商品の出荷作業を同じ場所で同時に行わないなどの工夫が必要です。
手書き伝票の場合は、商品や数量などを間違えて記載してしまうこともあり、こちらも注意しなければなりません。
こうしたヒューマンエラーをなくす物流のQCD改善については、こちらの記事で詳しく解説しています。
誤出荷・誤納品のリスクとは
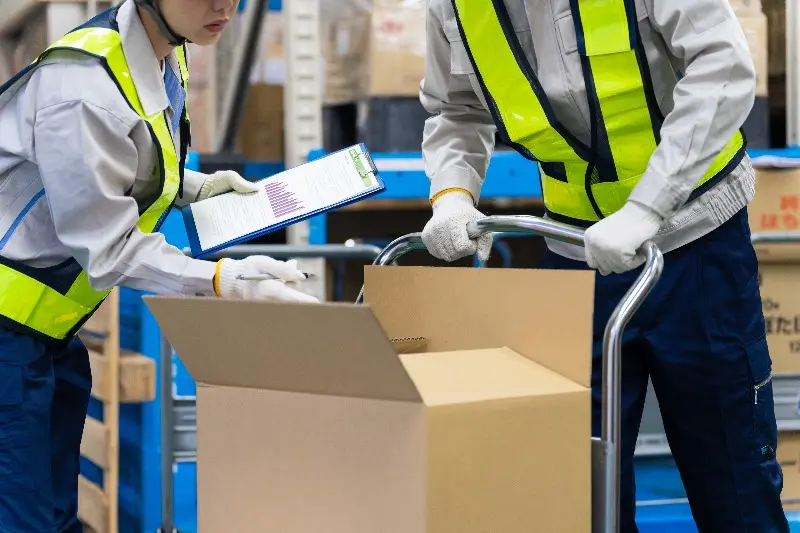
誤出荷が発生すると、以下のような様々なリスクが生じ、経営に悪影響を与えてしまいます。
顧客・取引先からの信頼低下
誤出荷は顧客からの信頼低下を招きます。商品の品質がどれだけ優れていても、誤出荷が頻発すると顧客にストレスを与え、取引したいという気持ちがなくなっていきます。信頼低下による販売機会の損失は経営にも悪影響を与えるでしょう。
また、信頼低下に伴いブランドイメージそのものに傷がつくこともリスクです。
個人情報の漏えい
出荷先を間違えると、
顧客の氏名や電話番号などの個人情報が誤出荷先の人物や会社に漏えいしてしまう可能性があります。個人情報が悪用され顧客が被害を受けてしまうと、最悪の場合訴訟に発展することもあります。
このように、個人情報の漏えいは顧客・事業者双方に大きなリスクを与えかねないため、十分に注意が必要です。
在庫情報との乖離
誤出荷が発生すると、
データ上の在庫と実態との乖離が発生してしまうリスクもあります。
たとえば、注文数が5個のところ、数え間違いにより6個の商品を出荷した場合、データ上の在庫数よりも実際の在庫数の方が1個分少なくなってしまいます。データ上の在庫の方が多いと実態よりも多くの注文を受け付けてしまい、出荷のタイミングになって商品が足りないことに気付く、という事態になりかねません。
ムダなコストが発生
誤出荷が発生すると再送のコストが発生してしまいます。返品を着払いで受け付けることも多々あり、
正しく出荷した場合に比べ数倍の配送料がかかってしまう可能性があります。
また、再送のための出荷作業や返品の受付、データ上と実際の在庫数量の確認と訂正などムダな作業が多く発生するため、人件費や時間の面でのコストも無視できません。
誤出荷・誤納品を対策するための流れ
さまざまなリスクをはらむ誤出荷を少しでも減らすためには、以下3つの対策が必要となります。
原因を確認する
まずは、
誤出荷の原因を確認することが何よりも重要です。どの工程で誤出荷が発生し、どのような部分に原因があるのかを正確に捉え、改善すべきポイントを明確にすることでミスを減らすことができます。
マニュアルを確認する
原因の確認とともに、マニュアルの確認も重要です。
マニュアルに沿って各フローの手順などを確認することで、どの工程に問題があるのか突き止めやすくなります。マニュアルがなければ直ちに入荷や検品、梱包などの作業ごとにマニュアルを作成し、各工程の手順やルールを確定して周知する必要があります。
システム導入より人によるミスをなくす
人手で作業をしている限りヒューマンエラーはなくならないため、
可能な限りシステム導入や自動化を推進する必要があります。
たとえば、ロケーションのシステム管理によって、在庫の保管場所を一目でわかるようにすることで、従業員の熟練度にかかわらず誰でもミスなくピッキングができるようになります。システムを導入することで、誤出荷の原因を正確かつ迅速に特定することができます。
LOGITOは誤出荷・誤納品の対策をするためのソリューションをご提案します
第一実業では、物流の自動化を図るソリューションサービス「LOGITO」を展開しており、総合機械商社としての豊富な知識や経験をもとに最適なソリューションをご提案しています。
今回ご紹介した誤出荷の対策として、
デジタルピッキングシステムとWMS(倉庫管理システム)があります。
デジタルピッキングシステムは、
デジタル表示器により自動でピッキング指示を行うソリューションであり、ポカミスをなくせるため、誤出荷対策に最適です。また、誰でもすぐに作業ができるため教育時間も大幅に削減し、紙の指示書が不要となることからペーパーレス化にも繋がります。
さらに棚搬送AGV(自動搬送車)と呼ばれるロボットを活用することで、ピッキング移動の手間を省くこともできます。
WMS(Warehouse Management System)は、倉庫管理を行うソフトウェア・アプリケーションです。WMSにより、
入出荷や工程を管理し、作業進捗の見える化などを行うことで、業務の標準化や効率化だけでなくコスト削減や在庫管理の強化も可能となります。
以下資料では、誤出荷を防ぐ物流自動化について解説しています。ご関心のある方はぜひダウンロードのうえご覧ください。
LOGITO 運営事務局
LOGITO 運営事務局では、全世界17カ国34拠点のグローバルネットワークにて培ったノウハウを生かし、物流自動化に関するトレンド・業界動向からノウハウ、成功事例まで、物流自動化の実践に役立つ様々な情報をお届けします。